CNC Turning Parts Manufacturer: Unlocking Precision in Metal Fabrication
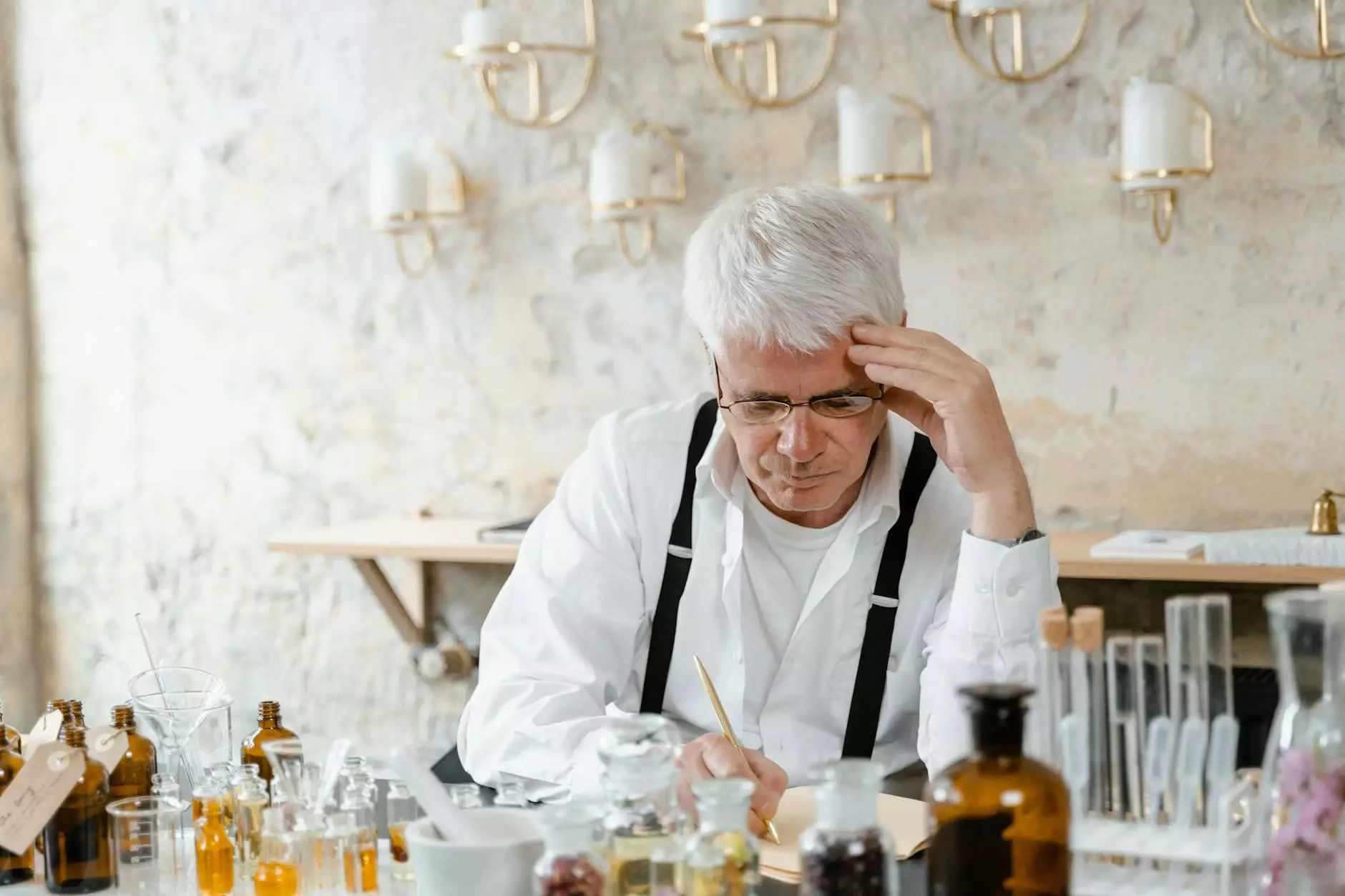
In today's fast-paced industrial landscape, efficiency and precision are paramount. When it comes to manufacturing metal components, these qualities are embodied in the role of a CNC turning parts manufacturer. This article delves into the intricacies of the CNC turning process, the benefits of utilizing these parts in your projects, and how collaborating with a top-tier manufacturer like DeepMould can elevate your business.
Understanding CNC Turning: What is It?
CNC turning refers to a computer-controlled process that shapes materials, primarily metals, into precise dimensions and designs. By employing a CNC lathe, the process allows for the rotation of the material against a cutting tool, resulting in smooth, exact shapes that are often required in various industries such as aerospace, automotive, medical, and many others.
The CNC Turning Process Explained
The CNC turning process involves several essential steps:
- Design Creation: Engineers create a detailed CAD (Computer-Aided Design) model of the desired part.
- Machine Setup: The CNC machine is set up with the appropriate tool and material is loaded.
- Programming: The CNC machine is programmed, often using G-code, which tells the machine how to move and operate.
- Turning Operation: The machine begins the turning process, cutting the material into the required shape according to the design.
- Quality Control: After machining, the parts undergo rigorous inspection to ensure they meet specifications.
Why CNC Turning Parts? The Advantages
Choosing CNC turned parts offers numerous advantages that can significantly benefit businesses:
- High Precision: CNC turning ensures tight tolerances and precision that manual methods cannot match.
- Reproducibility: Once a design is set, identical parts can be produced consistently, making it ideal for mass production.
- Complex Shapes: CNC turning can create intricate designs that would be difficult to achieve with traditional machining methods.
- Reduced Waste: The machining process maximizes material utilization, reducing waste and costs.
- Speed: CNC machines operate quickly, allowing for faster turnaround times on projects.
CNC Turning vs. Traditional Machining
Compared to traditional machining techniques, CNC turning offers superior benefits. While traditional methods rely heavily on the skill and precision of the operator, CNC machines operate through programmed instructions, which drastically reduces the chance of human error. Moreover, CNC turning can work continuously, leading to optimal production times without sacrificing quality.
Applications of CNC Turning Parts
CNC turning has a diverse range of applications across various industries. Some common uses include:
- Aerospace Components: Manufacturing components that require high precision and accountability.
- Automotive Parts: Creating engine parts, transmission components, and decorative elements.
- Medical Devices: Fabrication of surgical instruments and implants with stringent quality standards.
- Industrial Machinery: Production of parts for various machines and automation equipment.
Choosing the Right CNC Turning Parts Manufacturer
The selection of the right CNC turning parts manufacturer is critical to your project's success. When evaluating potential partners, consider the following factors:
1. Expertise and Experience
An experienced manufacturer, like DeepMould, will possess the knowledge required to understand the complexities of your specific industry. They should have a portfolio that demonstrates their ability to handle various materials and intricate designs.
2. Technology and Equipment
Advanced CNC machines equipped with the latest technology are essential for producing high-quality parts efficiently. Ensure the manufacturer utilizes modern machinery that can handle the specifications of your orders.
3. Quality Assurance
Implementing a robust quality control system is vital. Look for manufacturers who conduct rigorous testing and inspections at various stages of production to guarantee that every component meets your required standards.
4. Flexibility and Customer Support
A reliable manufacturer should be flexible enough to accommodate changes in design or production schedules. Excellent customer support is also key, ensuring that any questions or concerns are promptly addressed.
The Role of DeepMould in Metal Fabrication
At DeepMould, we pride ourselves on being a leading CNC turning parts manufacturer in the industry. We leverage cutting-edge technology paired with years of experience to deliver unparalleled quality and precision in every part we produce. Our capabilities extend to:
- Custom Manufacturing: Tailored solutions that meet individual client's needs.
- Rapid Prototyping: Quick turnaround times for prototypes, allowing faster product development.
- Comprehensive Support: Expert guidance throughout the entire manufacturing process, from design to delivery.
Future Trends in CNC Turning
As technology advances, the CNC turning industry is also evolving. Here are some notable trends to look out for:
1. Automation and Artificial Intelligence
The integration of automation and AI in CNC turning processes is revolutionizing production practices. Manufacturers can ensure consistent quality and optimize production schedules with minimal human intervention.
2. Advanced Materials
The development of new materials with improved properties will expand the possibilities for CNC turning. Manufacturers will need to adapt their processes to handle these materials effectively.
3. Sustainability Measures
As industries become more environmentally conscious, sustainable practices in CNC machining will gain prominence. This includes waste reduction techniques and energy-efficient machinery.
Conclusion: Empower Your Business with CNC Turning Parts
In conclusion, the role of a CNC turning parts manufacturer is crucial in today's manufacturing ecosystem. Companies that prioritize precision, efficiency, and adaptability will thrive in a competitive market. Partnering with an established manufacturer like DeepMould not only assures you of high-quality components but also gives you a competitive edge. Embrace the future of manufacturing with CNC turning—where quality meets innovation.