Discover the Power of Rapid Prototypes in Metal Fabrication
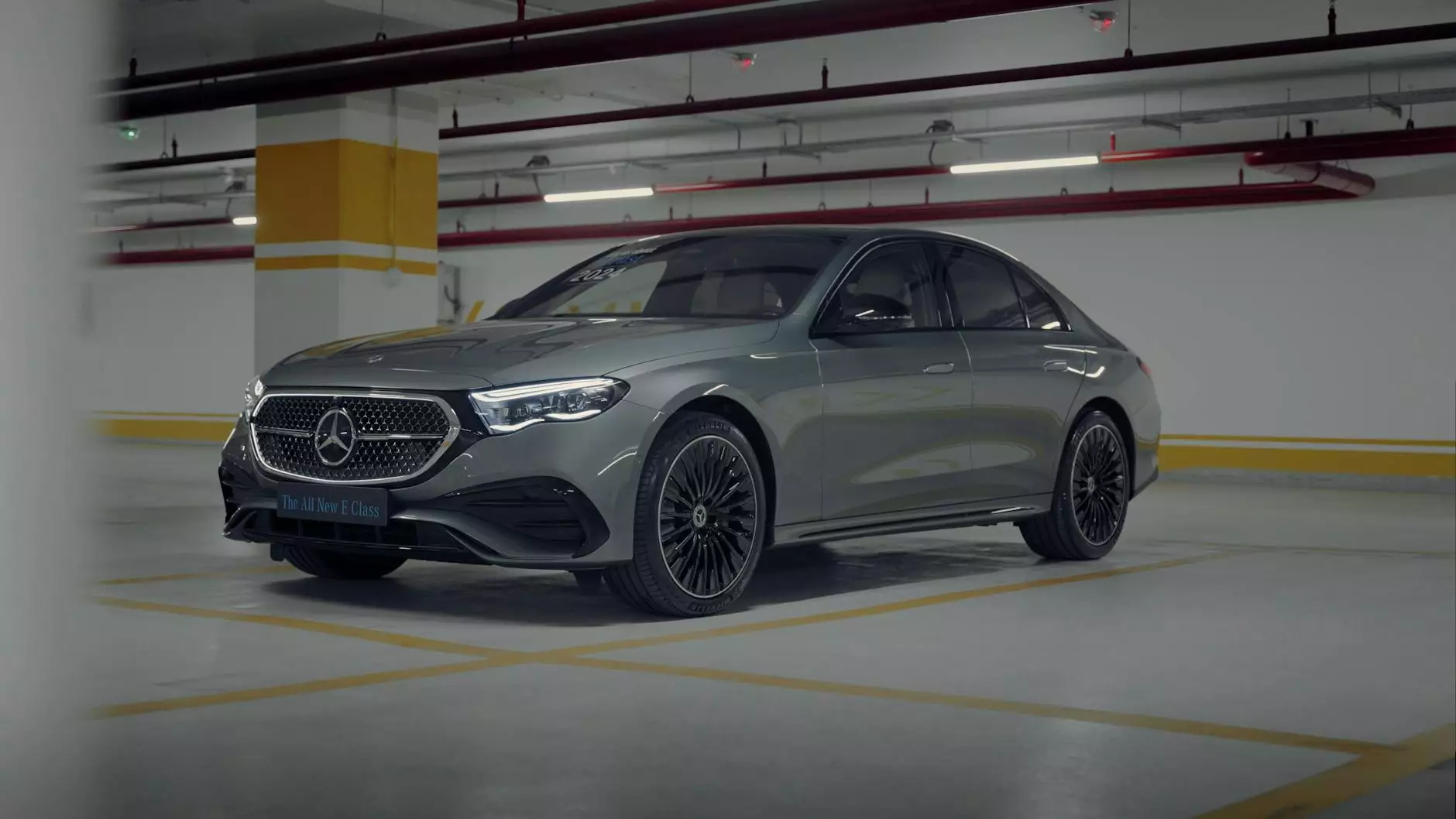
In today's fast-paced and ever-evolving world, the demand for rapid prototypes has grown exponentially. Particularly in the metal fabrication sector, these prototypes provide invaluable solutions that enhance production efficiency, encourage innovative designs, and ultimately lead to superior products. This article delves deeply into the realm of rapid prototypes, exploring their significance, applications, and benefits, especially through the lens of Deepmould.net.
Understanding Rapid Prototypes
Rapid prototypes are preliminary models created quickly to visualize, test, and iterate product designs. They utilize advanced technologies and materials, allowing manufacturers to create accurate representations of their final products in record time. Unlike traditional prototyping methods, which can be time-consuming and costly, rapid prototyping streamlines the product development process.
The Role of Rapid Prototypes in Metal Fabrication
In the context of metal fabrication, rapid prototypes play a crucial role. This industry traditionally relies on intricate designs and precision engineering, making the prototyping phase essential. Here are some ways rapid prototypes are transforming the metal fabrication landscape:
- Speed: Rapid prototyping significantly reduces the time required from conceptualization to production. Manufacturers can quickly develop and test metal components, ensuring faster project turnaround.
- Cost-Effectiveness: By minimizing waste and reducing the number of iterations needed during the design phase, rapid prototypes help lower production costs.
- Design Flexibility: These prototypes facilitate exploration of various design options, enabling engineers to refine and enhance their ideas before final production.
- Enhanced Communication: Rapid prototypes provide tangible models that improve communication between designers, engineers, and stakeholders, ensuring everyone is on the same page.
Key Technologies Behind Rapid Prototyping
The effectiveness of rapid prototypes stems from cutting-edge technologies. Here are some prominent methods used in metal prototyping:
1. 3D Printing
3D printing, or additive manufacturing, is one of the most revolutionary techniques in rapid prototyping. Through layer-by-layer construction, it allows for the creation of complex metal parts. Common materials include aluminum, titanium, and stainless steel, which are used to produce durable prototypes. The 3D printing process reduces material waste and enables intricate designs that would be impossible with traditional fabrication methods.
2. CNC Machining
CNC (Computer Numerical Control) machining is another vital technology in rapid prototyping. It involves using computer-controlled machines to accurately remove material from a solid block, resulting in precise metal parts. CNC machining is ideal for producing functional prototypes that require specific tolerances and surface finishes.
3. Metal Casting
While metal casting is a traditional method, it can be adapted for rapid prototyping. Techniques like vacuum casting or investment casting allow manufacturers to create prototypes quickly. These methods are particularly useful for producing larger parts or complex geometries that require durability and strength.
Benefits of Using Rapid Prototypes in Metal Fabrication
The integration of rapid prototypes in metal fabrication enhances product development processes significantly. Here are some of the primary benefits:
- Faster Time-to-Market: With the ability to quickly iterate designs, products can reach the market faster, giving companies a competitive edge.
- Improved Quality: Rapid prototyping allows for thorough testing and validation, reducing the risk of defects in the final product.
- Customization: Manufacturers can easily modify prototypes based on client feedback, leading to tailored solutions that meet specific client needs.
- Reduced Risk: Investing in rapid prototyping minimizes financial risks associated with large-scale production of untested designs.
The Future of Rapid Prototypes in Metal Fabrication
As technology continues to evolve, the future of rapid prototypes in the metal fabrication sector looks promising. Innovations such as artificial intelligence, machine learning, and advanced materials science are paving the way for more efficient, sustainable, and versatile prototyping methods. Here are some anticipated trends:
1. Increased Automation
Automation is set to enhance rapid prototyping processes further, allowing for a combination of speed and accuracy that is hard to achieve manually. This will lead to decreased production times and lower labor costs.
2. Greater Material Variety
Ongoing research into new materials will enable the use of a wider range of metals and composites in rapid prototyping. This diversification will expand application possibilities, allowing for stronger and lighter prototypes.
3. Sustainable Practices
The push for sustainability in manufacturing practices will influence rapid prototypes as well. Eco-friendly materials and processes will become standard, aligning with global efforts to reduce carbon footprints.
Conclusion
In summary, the impact of rapid prototypes in the metal fabrication industry is profound and transformative. They represent a shift toward faster, more efficient, and innovative product development methods. Companies like Deepmould.net are at the forefront of this revolution, leveraging cutting-edge technologies to fulfill the growing demands of their clients while promoting quality and sustainability.
As the industry progresses, embracing rapid prototypes will be crucial for businesses seeking to maintain a competitive edge and drive innovation in their product offerings. The future is bright for metal fabricators who adopt and adapt these advanced methodologies, ensuring they remain leaders in their field.