The Profound Impact of Plastic Injection Tooling on Metal Fabrication
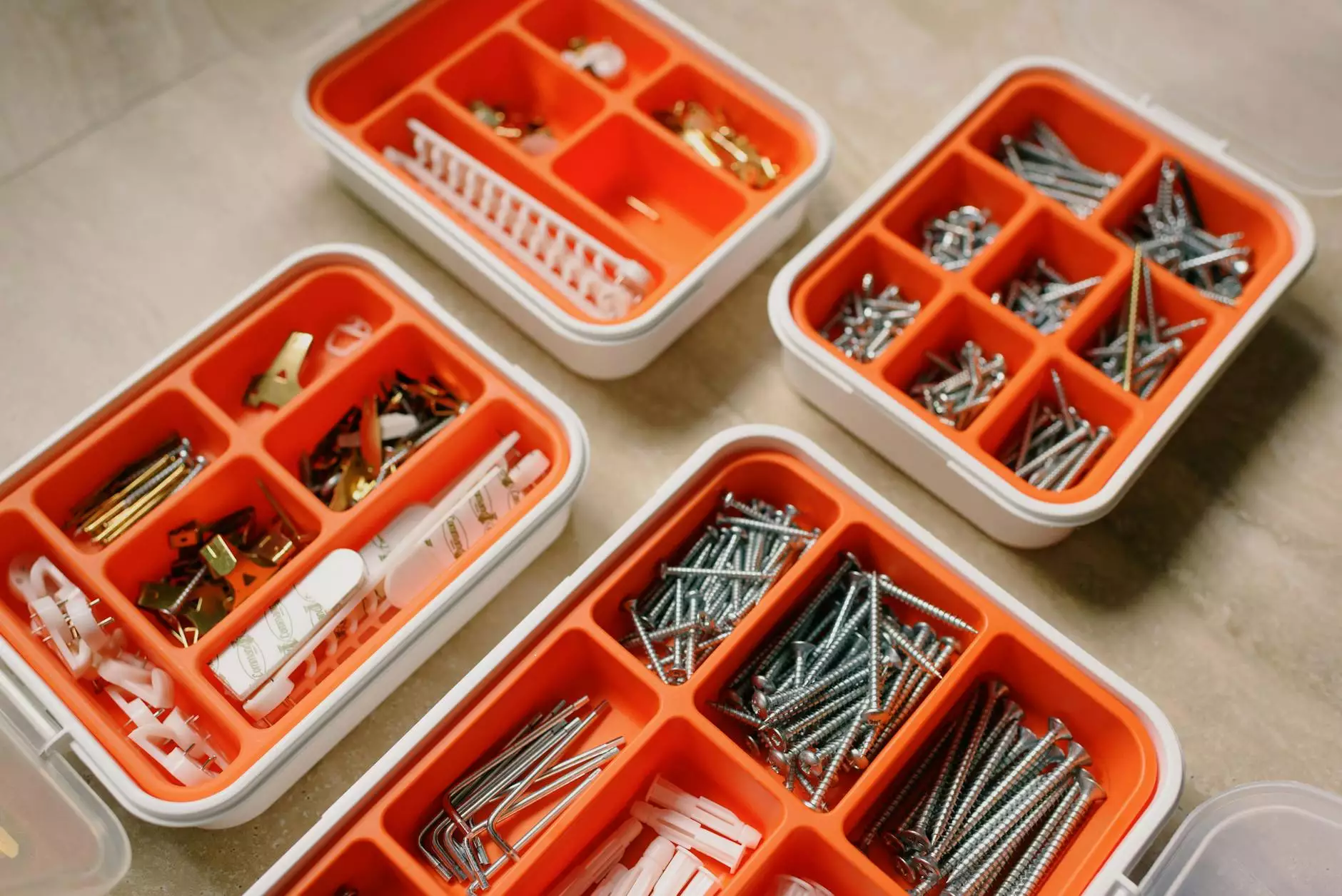
In today's highly competitive manufacturing landscape, every business seeks to enhance productivity, reduce costs, and maintain exceptional quality. Among the pivotal techniques that bolsters this objective is plastic injection tooling. This transformative technology not only streamlines production but also elevates the overall quality of the end products, paving the way for businesses to thrive in the industry.
Understanding Plastic Injection Tooling
Plastic injection tooling is a manufacturing process used to create plastic parts by injecting molten plastic materials into a mold. This method allows businesses to fabricate complex and high-precision components that are essential in various industries, including automotive, consumer goods, and electronics. This technology plays a crucial role in shaping the future of manufacturing and serves as a cornerstone for efficient metal fabrication processes.
Advantages of Plastic Injection Tooling
There are several significant advantages to employing plastic injection tooling in manufacturing:
- High Efficiency: This method allows for the rapid mass production of parts, significantly reducing cycle times.
- Precision and Accuracy: The molding process ensures that products are made to exact specifications, minimizing defects and wastage.
- Cost-Effectiveness: Although initial setup costs can be high, the long-term production costs are lowered due to the high efficiency and low scrap rates.
- Design Flexibility: Complex shapes and designs can be easily achieved, allowing businesses to innovate and customize products.
- Material Versatility: Various types of plastic materials can be used, providing options for different applications.
The Role of Plastic Injection Tooling in Metal Fabrication
When integrating plastic injection tooling with metal fabrication, businesses can harness the strengths of both materials. While traditional metal fabrication techniques offer durability and strength, the incorporation of plastics can enhance functionality while reducing weight. This synergy is particularly advantageous in industries where both materials are used to optimize product performance.
Key Applications in Various Industries
Plastic injection tooling is revolutionizing various sectors. Here are some key applications:
1. Automotive Industry
The automotive sector is one of the largest consumers of plastic injection tooling. Components such as dashboard panels, bumpers, and connectors are molded using this technique, significantly reducing vehicle weight and improving fuel efficiency. Companies that embrace this technology can produce intricate parts that meet stringent safety and performance standards.
2. Consumer Goods
From toys to household appliances, plastic injection tooling is instrumental in manufacturing consumer products. Its ability to produce complex geometries enables the creation of unique designs that appeal to consumers, ultimately leading to increased sales and customer satisfaction.
3. Electronics
In the electronics industry, precision is paramount. Plastic injection tooling allows manufacturers to produce enclosures, connectors, and components with fine tolerances, essential for the functionality of devices such as smartphones, tablets, and computers. The lightweight nature of plastic also contributes to the portability of electronic devices.
How to Choose the Right Plastic Injection Tooling Partner
Selecting an appropriate partner for plastic injection tooling is critical for ensuring success. Here are some factors to consider:
- Expertise and Experience: Look for a company that has substantial experience in plastic injection molding and understands the nuances of your industry.
- Technology and Equipment: Ensure the manufacturer has state-of-the-art machinery and technology that can meet your production needs.
- Quality Assurance: Investigate the company's quality control processes to ensure they adhere to industry standards.
- Customer Support: A reliable partner should provide excellent customer service and support throughout the product development process.
The Future of Plastic Injection Tooling in Metal Fabrication
As industries evolve, so does the significance of plastic injection tooling. Advances in technology, such as the integration of computer-aided design (CAD) and automation, are set to revolutionize the manufacturing process. Improved materials and innovative molding techniques will enable fabricators to produce even more complex and high-quality components.
Conclusion
In conclusion, plastic injection tooling is more than just a manufacturing technique; it is a catalyst for innovation and efficiency in the metal fabrication sector. By combining the strengths of plastic with traditional metal processes, businesses can create products that are not only high-quality but also tailored to meet the evolving needs of consumers. As industries continue to advance, the role of this technology will only become more integral to their success. Adopting and mastering plastic injection tooling may just be the leap forward that propels your business into the forefront of the competitive landscape.
For more information on plastic injection tooling and its applications, visit Deep Mould.